
Ultrasonic piezo motors provide very high speed and are typically not used when nanometer level and sub-nanometer level precision is required. Inertia type piezo motors are compact, low cost motors with relatively low force.įlexure-guided / motion amplified actuators provide shorter travel ranges but very high resolution and can be used for continuous scanning applications. In this paper, we present a frequency domain method for open-loop control of three-dimensional dynamic motions of piezo-stack actuators. the system dynamics are essentially single degree of freedom. Travel ranges are typically 10 m to 200 m. These motors make use of continuous clamp/unclamp and expand/contract cycles of a number of piezo elements. The voltage control response of the piezoelectric actuator tested was demonstrably more. Piezo Stack Linear Actuators provide high resolution, high power, very rapid response ( seconds). For high force and long travel, piezo-walk type motors are recommended. Piezo nanopositioning motors are based on different drive principles. Two design examples are presented which illustrate the effect of the stiffness of the external spring and the size of the design domain on the topology of the solution.Nanopositioning Motors, Piezo Actuators XYZ Stages Single Axis Stages 6-Axis Stages Tip/Tilt Stages The optimization problem formulation, finite element implementation, solution algorithm are discussed. Piezoelectric actuators are popularly applied as actuators in high precision systems due to their small displacement resolution, fast response and simple construction. In this paper an improved formulation is presented where the piezoelectric properties and stiffness of the stack are included along with an external spring representing a resisting load the actuator is working against. However, it is well known that the best actuator performance occurs when the stiffness of the stack is considered and matches the stiffness of the surrounding coupling structure.

.jpg)
heat transfer from the surface of the piezo-ceramic stack.
#DYNAMIC RESPONSE OF STACK PIEZO ACTUATORS FULL#
Previously the optimization was done assuming that the stack actuator provided a constant unit load to the compliant mechanism. In this chapter a full electromechanical model of piezoceramic actuators is presented. piezo-actuators deployed in SRF cavity tuners operated at high dynamic voltage range rate. Two design examples are presented which illustrate the effect of the stiffness of the external spring and the size of the design domain on the topology of the solution.ĪB - A topology optimization method for design of compliant mechanical amplifiers for piezoceramic stack actuators is presented. The optimization problem formulation, finite element implementation, solution algorithm are discussed. In addition to the complex three-dimensional nature of their motions, the piezo-stack actuators have been shown to exhibit non-linear response behavior such as hysteresis, drift, creep, and time delay 6, 7. Previously the optimization was done assuming that the stack actuator provided a constant unit load to the compliant mechanism. Depiction of a typical multi-axis piezo-stack actuator. Multilayer piezoelectric stack actuators are widely used in many industrial applications and the investigation on the dynamic behavior of this element is needed.
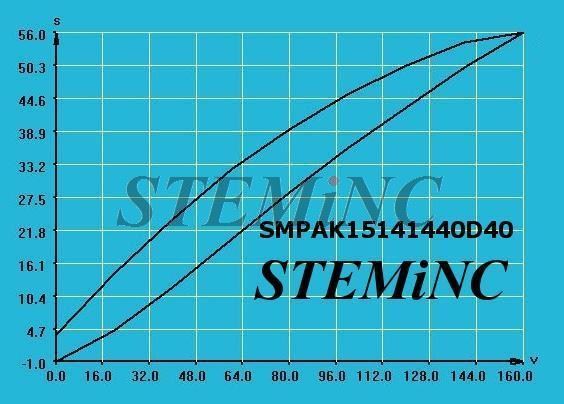
N2 - A topology optimization method for design of compliant mechanical amplifiers for piezoceramic stack actuators is presented. The authors gratefully acknowledge the support of National Science Foundation Division of Design, Manufacture, and Industrial Innovation grant number DMI-9870527. T1 - Design of compliant mechanical amplifiers for piezoceramic stack actuators considering stiffness properties
